11/28/2006 update:
This past weekend I did indeed get some “me” time to work on my bot. I spent most of Friday making the cables and soldering the interface board. I decided to use ribbon cable (old IDE cables) for the point to point wiring versus wire wrap. I really like the way it worked out and can recommend other give it a try too.
I decided against creating four 8-pin cables from the port headers on the MAVRIC to my interface board. Instead, I designed it so that I used all of PortB for one cable and a combination of PortF, PortE and PortD for the other. In other words, I went the wiring harness route.

From left to right, simple switcher power supply, MAVRIC, interface board, encoder, DC gearmotor
I also decided against reusing my tank base for this bot. The vacuum cleaner belts were starting to dry rot and I really wanted to redo the mechanics of the drive. I spent the rest of my weekend looking for solutions to couple the motors, wheels, and encoders. When I finally settled on gears I then began the search for affordable gears. www.servocity.com have a nice selection, but they are very proud of their gears. $4.95 for 1 gear and it doesn’t even have a set screw not is it bored for the ¼” shaft. Instead they want to sell you a hub for another $4.95. I have a micro lathe and can make my own hubs, but $4 is too much for a single gear IMHO. I found Stock Drive after trying www.servolink.com (great prices but $30 minimum order) and MSC (no details on the gears). They hit me with a $3.95 handling charge for using the online store and then another $6.18 for UPS for 4 freaking gears. The gears were reasonably priced at $2.10 a piece. If they had offered USPS I would have picked that. It’s a major pet peeve of mine getting overcharged for shipping. But I digress.
Oh, and I also ordered some wheels ($10 minimum order) from www.budgetrobotics.com . After deciding on the gears, I was able to knock up a model in CAD. The silver motors will be aligned with the center of the 9" diameter disk platform. The red encoders will be linked via the gears. The wheels will be attached to the gear on the motor shaft via 4 screws. I am planning for the gears to be a press fit, but if not, the hubs on the gears or thick enough to drill and tap for a set screw. Failing that, I'll bore out the hub and make a sleeve hub out of aluminum.
Onward,
Jay
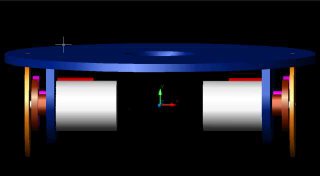
This iso wireframe shows how the gears come into play. The base is made from 6mm pvc.
